Download Resource
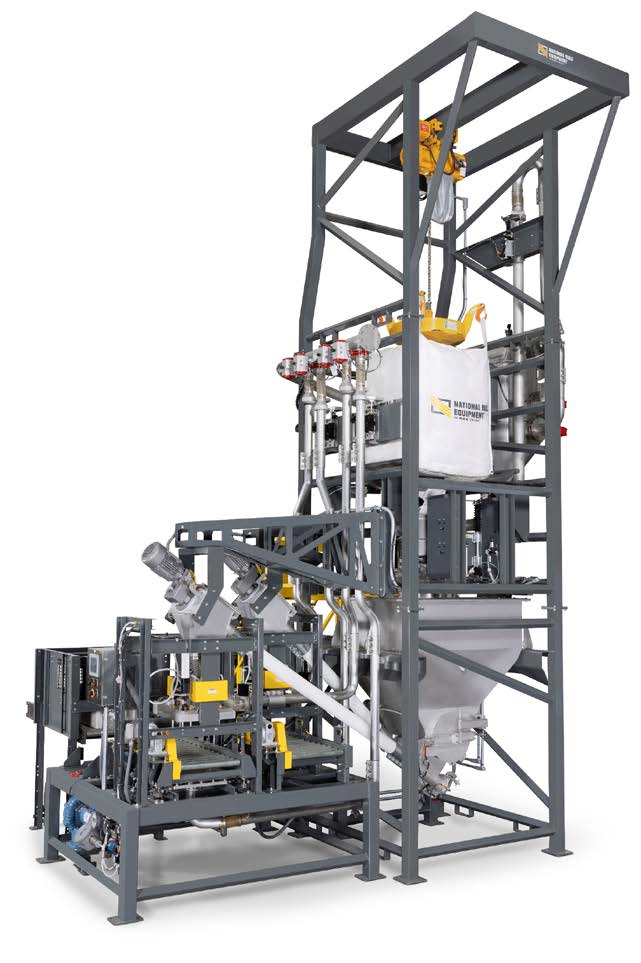
Bulk Bag Discharger with Dual Screw Transfer and Dual Container Fill Station for Aluminum Oxide
NBE was asked to evaluate an existing bulk bag discharger that a customer had repurposed and was experiencing rate and severe "house cleaning" issues. The existing bulk bag discharger was not designed to handle the challenging characteristics of aluminum oxide. The main issues are picking up and transferring the material as well as lacking any type of dust containment. The discharge of the screw conveyor included a cardboard fabricated dust collection hood over a container fill station. After our on-site evaluation, we completed material testing at our Innovation Center to further analyze the aluminum oxide handling issues and completed material transfer (rate) and densification testing. NBE was asked to provide dust collection, increase throughput and maximize the material volume in each container. To increase the rate, we supplied an agitator hopper, dual discharge screw conveyors feeding two separate fill stations that included independent scales. A central dust collection system located on the bulk bag discharger was provided to control and reclaim any captured dust. The NBE system is filling 33%more material per container and double the throughput. Understanding the application requirements, NBE conducted a test with the customer at our Innovation Center and Application Workshop. We used a bulk bag discharger with integral lump breaker (with screen), along with a screw conveyor, to unload the bag and process it into a consistent supply of material. The salt was broken down back to nearly original particle size. The customer was thrilled with the outcome.