Download Resource
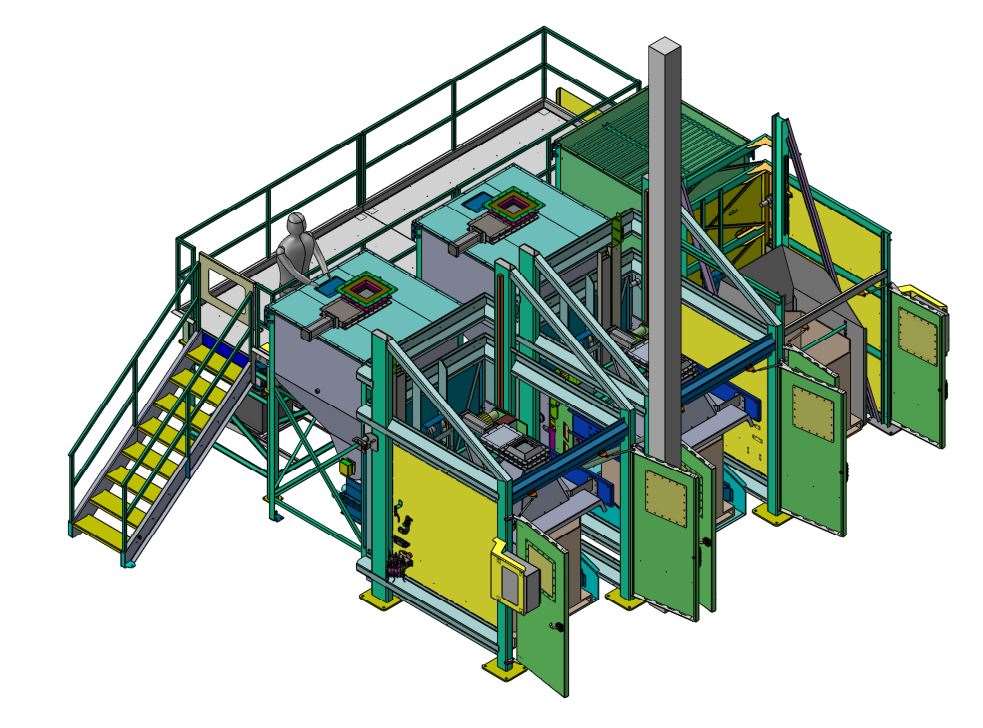
Container Discharger System for PET, PP Plastic Chop Trim, Plastic Flake, Plastic Pellets
This customer's overall scope involved handling three different materials, each with different properties, some dusty, delivered in varying container sizes, to be pneumatically conveyed to downstream molding equipment. A compact footprint was required to maximize plant space and operator safety during operation and maintenance was also essential. For the chop/trim/flake products, lift and seal dischargers were incorporated into the system. The hood seals to the top of the container prior to rotation, and mate with the surge bin through 12-inch roller gates that open when rotation is complete. This allows the entire contents of the container to empty with a sealed/ dust free connection. These receiving bins also are equipped with agitation inside the hoppers to promote flow and the product also passes through a light duty crumbler prior to entering the conveying line. For the pellet product, a high lift and discharger unit was used. Dust was not a concern, so the receiving bin had an open top with a grate incorporated to catch large debris. A mezzanine was added to give operators access to the equipment and for maintenance. For safe operations, a laser scanner on the mezzanine was included to disable the discharger/slide gate when obstructed, preventing operator injury when in motion. Safety caging and interlocked access doors on the loading side prevent operation when not closed.